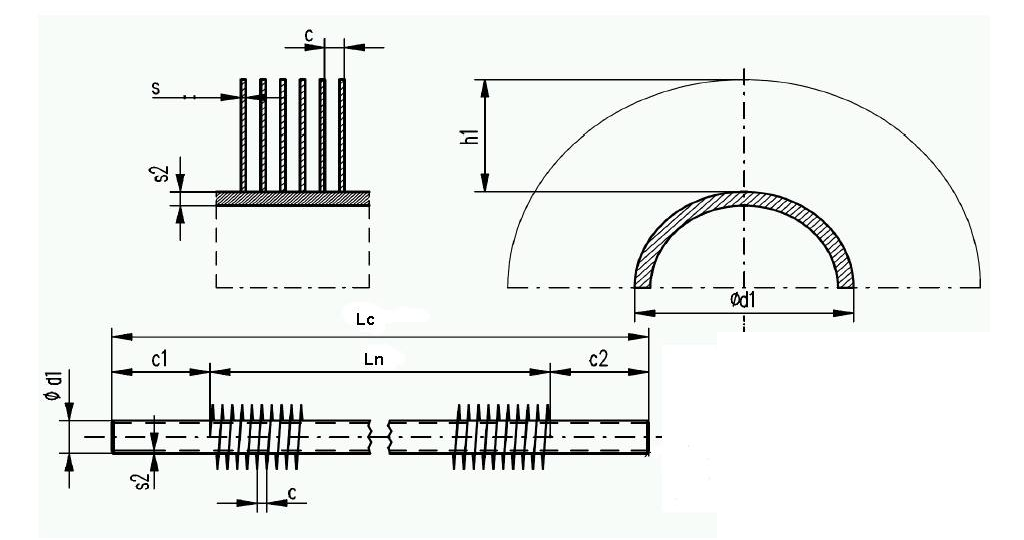
Typical Tube Dimensions*
Diameter: from 15 – 63.5 mm
Length: up to 21 m
Height of fin: up to 0.50 x tube OD
Fin thickness: 0.6 mm to 1.5 mm (serrated fin: max 1.2 mm)
Fins per inch/meter: up to 500 fins / meter (depends upon fin thickness)
Grade fin material: Carbon Steel, Inconel, Stainless Steel, inquire*
Tube material: Carbon Steel, Alloy Special Steel, CrMo, Inconel, inquire*
Imperial and metric units are acceptable
Standard documentation: English, German or Polish (other: please inquire)
*Please note: Alternate grades and requirements can be available. May require additional technological tests
Conditions of acceptance
Linear dimensional tolerance for tubes is according to EN ISO 13920 - class B
When drawings are supplied by the client, drawing tolerances will be in force
Tolerance of fin tubes (outside diameter: tube and fin): 0 +/- 2 mm. When drawings are supplied by the client, drawing tolerances will be in force
The following welding tolerances are acceptable:
L ≤ 5000 mm
Weld gap shall not exceed 2.5% per meter of fin
Weld gap shall not exceed 2.0% on total length of fin
Distance between 2 intervals (weld gaps) cannot be less than 150mm
Start and finish of the fin must be welded / tack welded
Length of the gap / weld discontinuity for a pipe:
5000 < L ≤ 10000 mm
Weld gap shall not exceed 2.0% per linear meters of fin
Weld gap shall not exceed 1.65% on total length of fin
Distance between 2 intervals (weld gaps) cannot be less than 200mm
Start and finish of the fin must be welded / tack welded
Length of the gap / weld discontinuity for a pipe:
L > 10000 mm
Weld gap shall not exceed 2.0% per linear meters of fin
Weld gap shall not exceed 1.5% on total length of fin
Distance between 2 intervals (weld gaps) cannot be less than 200mm
Start and finish of the fin must be welded / tack welded
Notes:
Applied laser welding technology provides a metrollogical bond between fin and surface of the pipe. This process ensures a continuous metallic connection of the fin material with pipe material and thereby improving heat transfer efficiency
The welding process provides a weld with full penetration (evaluation of the weld according to point 3 of this instruction)
The quantity of spatters has reduced to a minimum in comparison with fin tubes produced by GMAW method (MAG-Metal Active Gas) and HFW High Frequency Welding
In cases where these instructions do not cover a given regulation, VGB Power standards are valid: VGB PowerTech
The scope of test process:
Prior to production:
100% visual test of the materials
Macro test
Hardness test HV1 (HV5)
During production:
Continuous 100% visual exam
Every 100 finned tubes receives a macro test (additionally for material group 4, 5 and 6 hardness test)