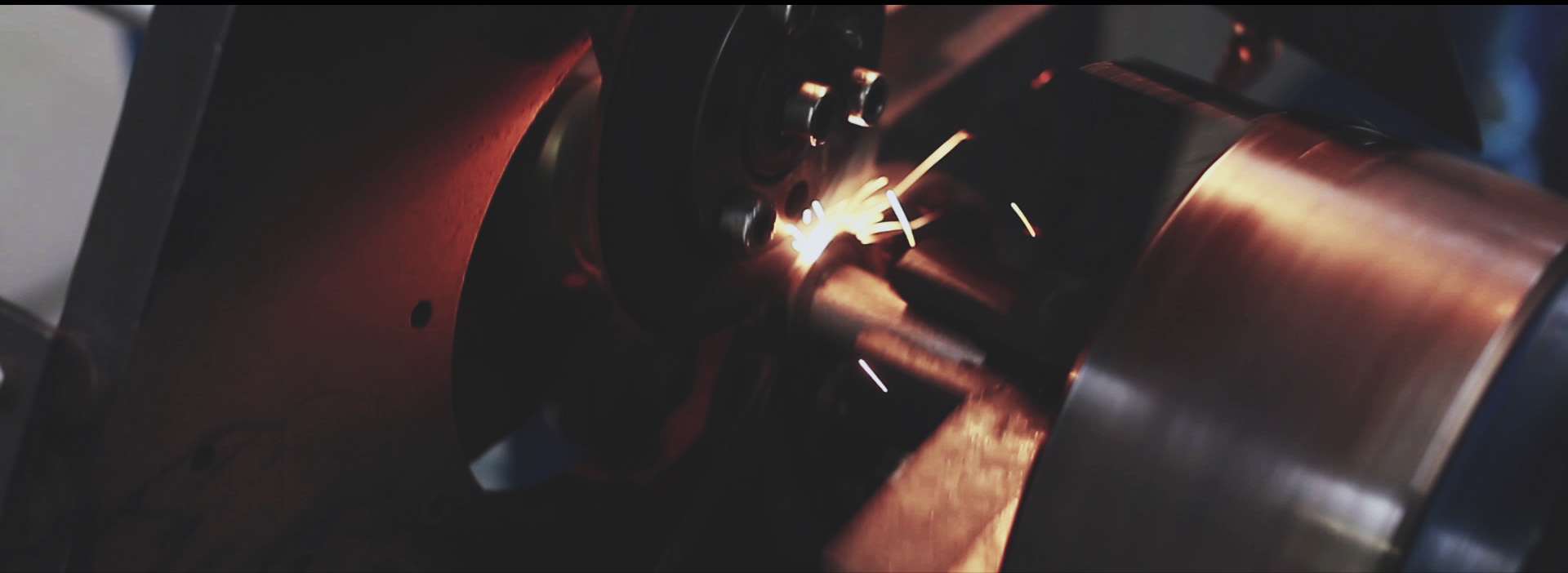
Most Efficient:
Making thermal calculations does not have to involve an added weld wire or its splatter and so contributes and promotes to greater heat transfer efficiencies
MAG
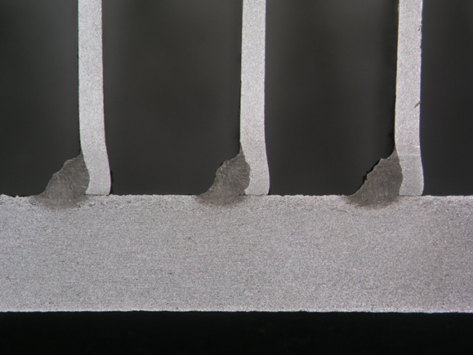

Laser
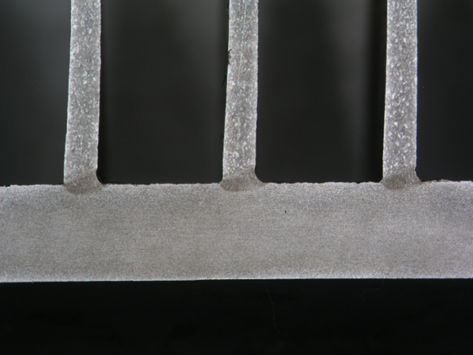
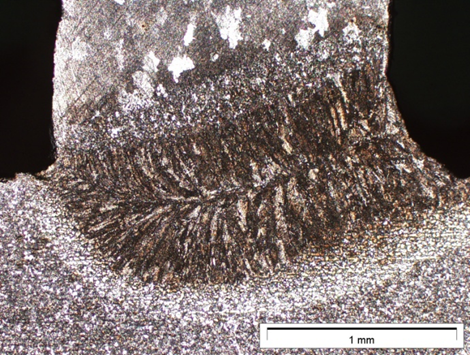
Lighter:
Because the laser process does not use a foreign weld wire, there is no added weight. Only the fin or rib and the pipe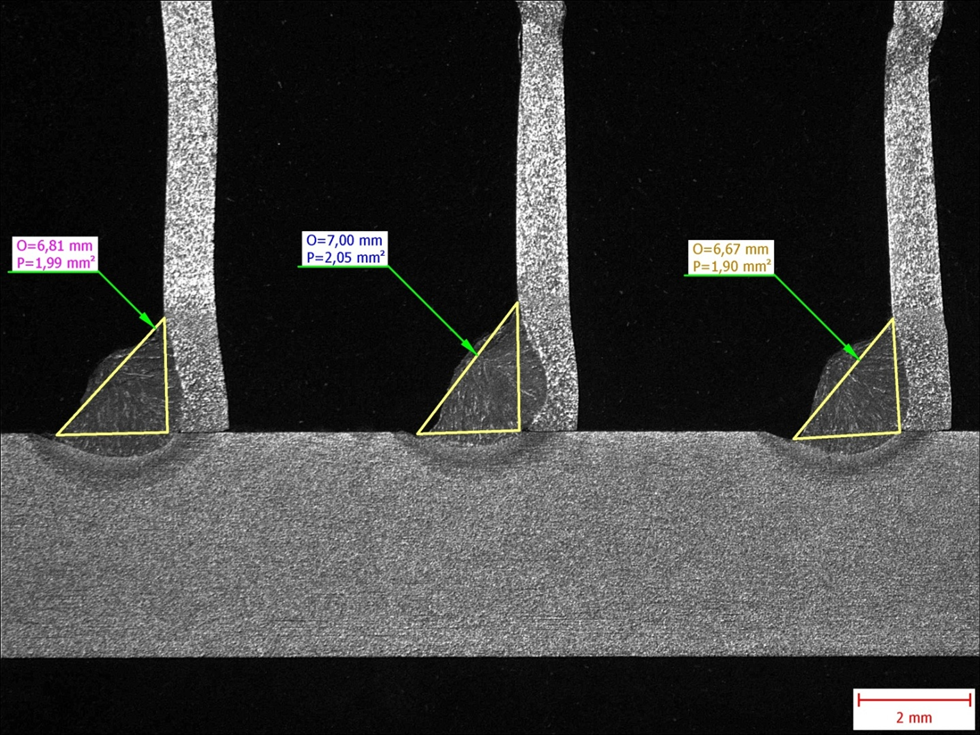
The measured difference in surface area is 2mm2, multiplying this by the length of the weld we get a saving on weight per 1 meter 0.76 kg. or .51 lbs. per foot
Full Penetration of Weld:
Due to the laser process, the entire length of the fin and pipe become “one metal” as there is no added weld wire or the required shield gas for the welding process.HF
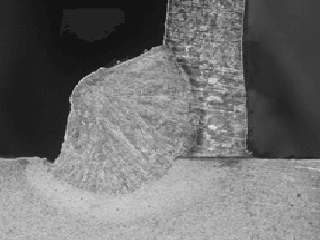
Poor connections also cause problems when calculating the efficiency of the heating system
Laser
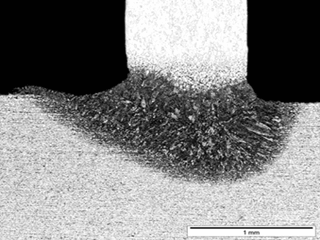
When calculating the efficiency of the system, the thickness of the rootcan be used for making the pipes can beassumed.
No Gap Between Fin and Pipe Wall:
There is no void between the fin root and pipe wall which can cause crevice corrosion, an attack that usually takes place in a very tight gap between two surfaces. The gap can promote cold spots and therefor corrosion.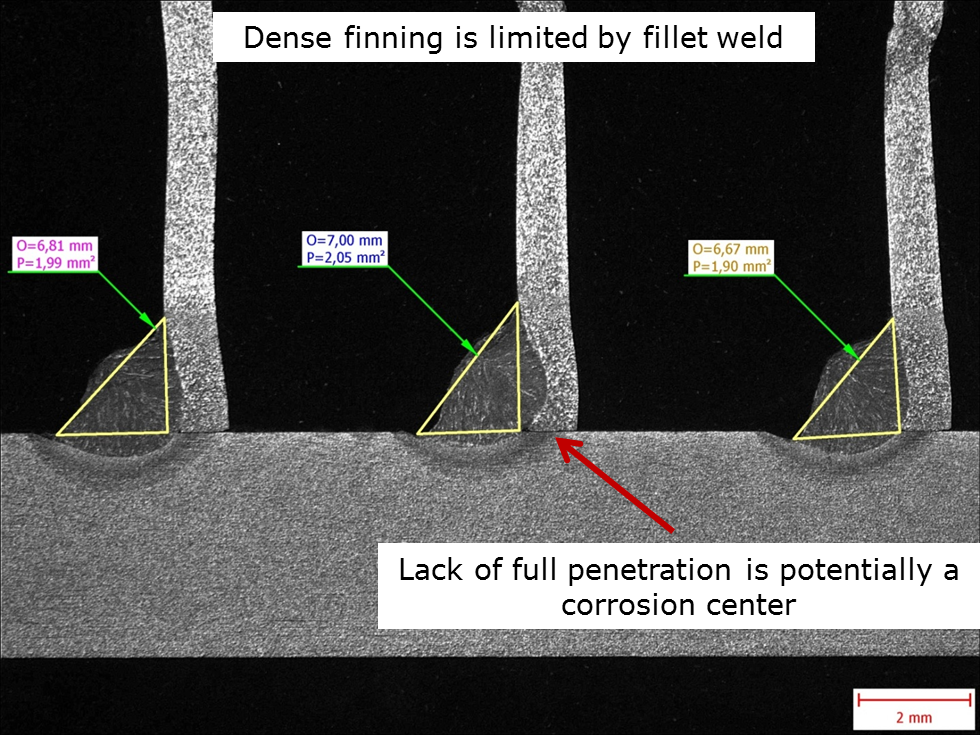
Gap can lead to “crevice corrosion”
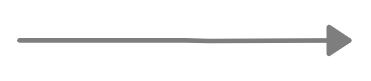
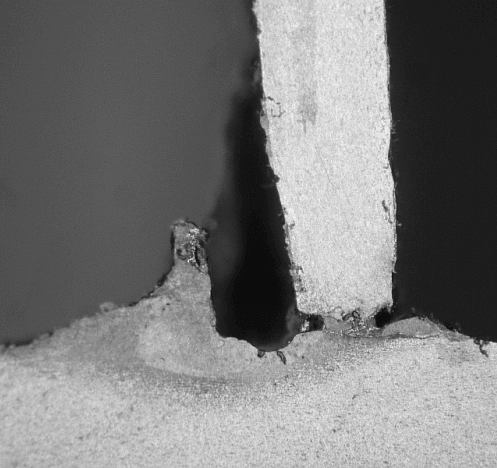
Precise, Distortion Free Welds:
Laser is precision tuned without interference of wire or shield gas. Complete melt of the fin to pipe connection along the entire length of the finBetter Weld Control for Joining Dissimilar Metals:
Precision tuned per applicationLess Splatter:
Cleaner and smoother surfaces will promote better heat transfer, less pressure drop and less opportunity for particulate buildup, no matter how small the blemishes appear to be.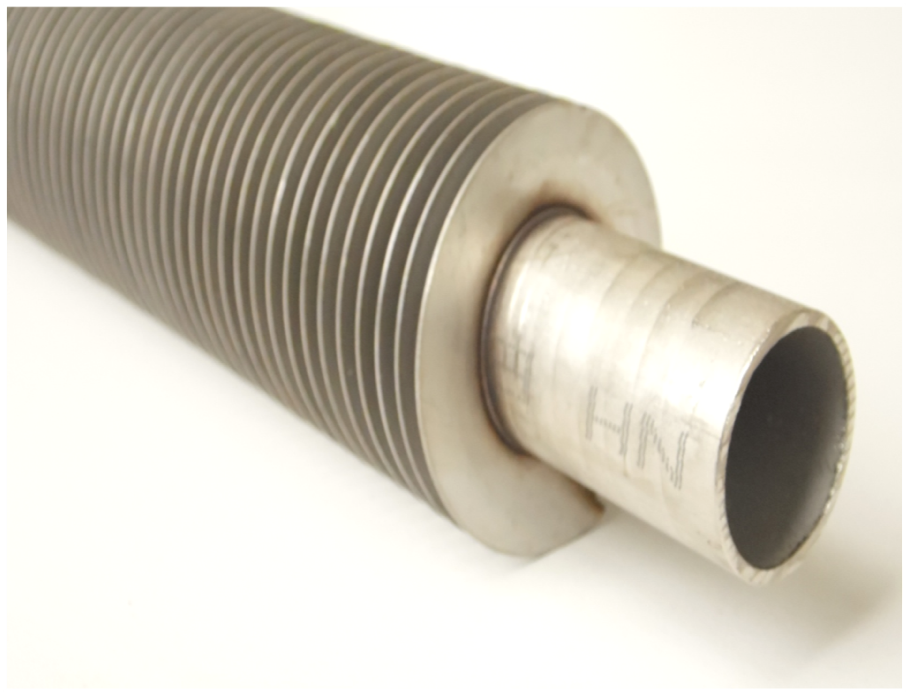
Uniform Root Hardness:
Other welding methods can leave uneven hardness throughout the fin to pipe configuration.HF
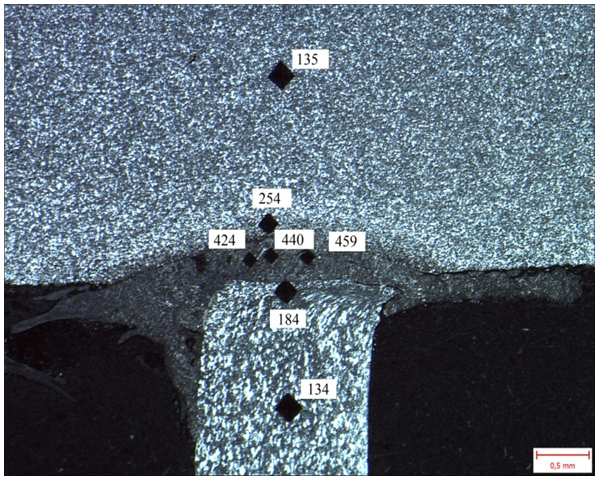
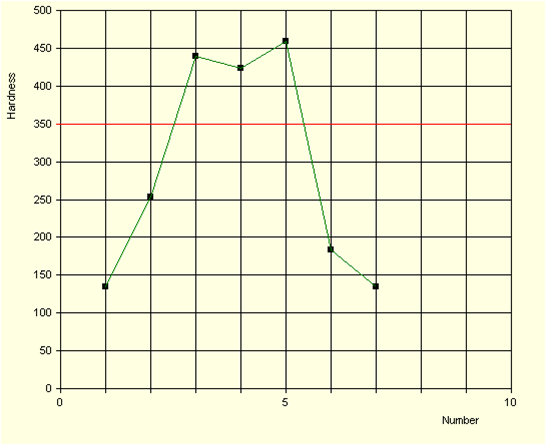
Hardness values (HV) significantly exceeds the allowable values allowed for pressure equipment (max. ≥ 380 HV)
Laser
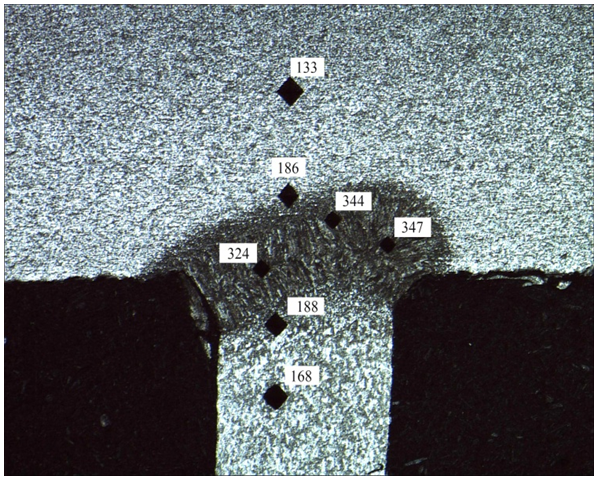
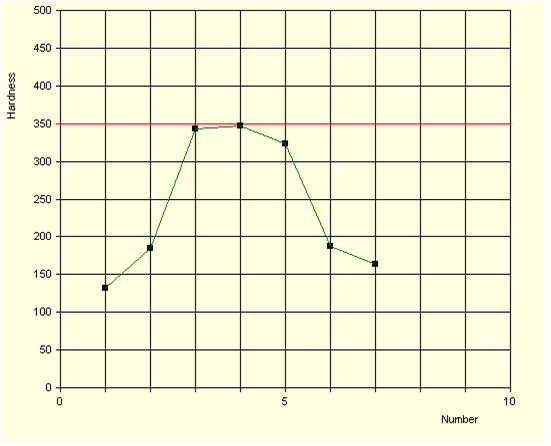
Hardness values (HV) does not exceed the allowable values allowed for pressure equipment (max. ≥ 380 HV)
Pass The Strength Test:
MAG

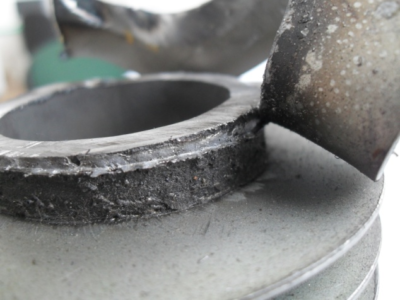
Due to the poor quality of the connection between the tube and fin, a proper rupture test cannot be made. In this instance, simple gripping tools were used to pull the fin away from the tube. In some cases, during a cutting trial, the fin broke away easily from the tube.
MAG
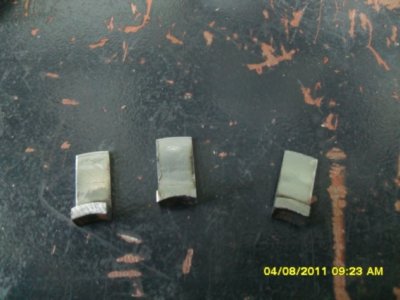
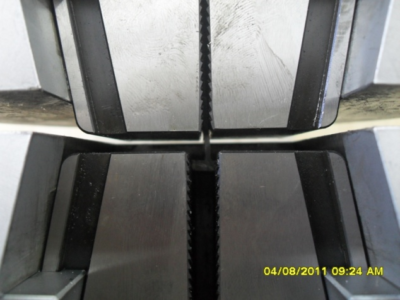
Tensile testing of laser welded samples showed that all samples broke in the tube material and not at the weld. Proving the high quality of the weld joint. The average tensile strength is 320Mpa / 3200 bar.div>
From a manufacturing perspective:
Laser welded finned tubes are manufactured and comply with the highest requirements
Does not require the use of welding wire
Elimination of shielding gases in the welding process
Improved manufacturing efficiencies
The manufacturing process is designed to operate in continuous production mode which translates into no interruptions in the technological process as required.
All lead to significant reduction of manufacturing costs
Video:
Processing lines of finned tubes laser welding can be assembled into production line systems in order to increase the production capacity.
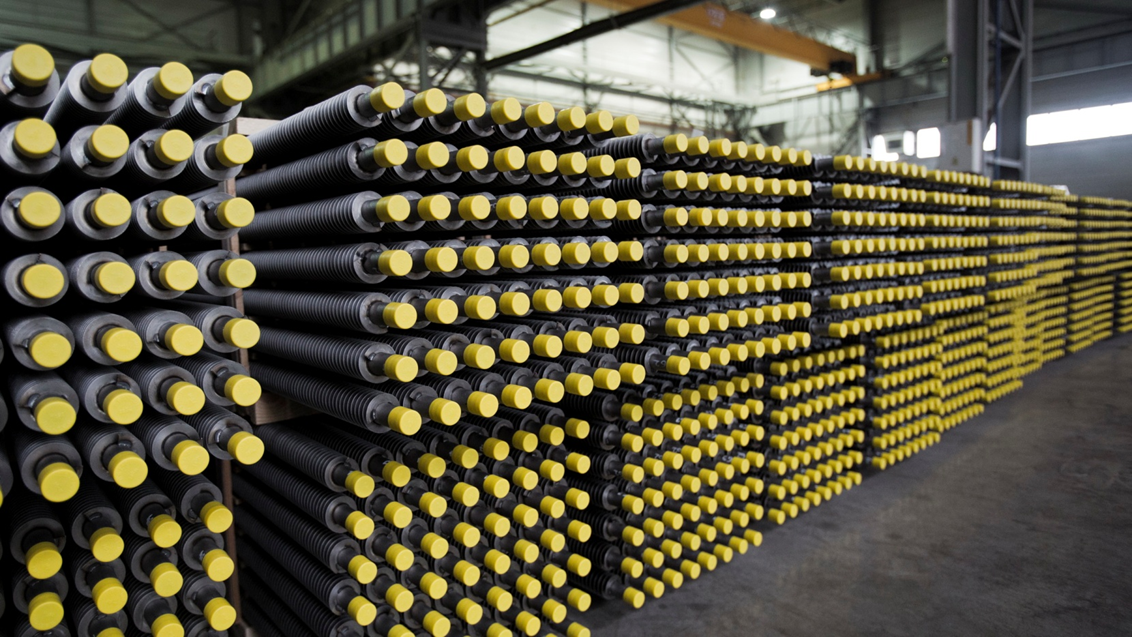